Embark on a captivating journey into the heart of Kutani ceramic artistry with a visit to the Cerabo Museum. This insightful article delves into the meticulous process of creating these exquisite Japanese ceramics, from the sourcing of unique, finely-grained stone to the intricate painting and firing techniques. Discover the secrets behind the enduring strength and distinctive character of Kutani ware, a legacy honed over generations of skilled artisans. We explore the museum's impressive collection, showcasing the diverse styles and innovative techniques that make each piece a unique work of art.From the initial meticulous preparation of the clay, involving hours of grinding and purification, to the diverse shaping methods and multiple firing stages, each step is a testament to the dedication and precision of the Kutani craftsmen. The Cerabo Museum provides a window into this rich tradition, highlighting the artistry and ingenuity involved in transforming raw materials into breathtakingly beautiful and durable ceramics. Prepare to be amazed by the intricate details, vibrant colors, and enduring elegance of Kutani ware.
Pros And Cons
- Made with fine clay particles creating strong vessels
- Unique process involving multiple firings and coatings
- Artisanal production with various decorative techniques
Read more: 9 Exquisite Japanese Ceramic Coffee Cups
The Raw Material: Kutani Stone
The creation of Kutani ceramics begins with a unique stone, unearthed near the area. This stone, possessing incredibly fine particles, is a key element in achieving the strength and character of Kutani ware. Its revival in the late Edo period contributed significantly to the development of this distinct pottery style. The finely ground particles bind together to form an exceptionally strong material for the ceramic pieces.
This stone is carefully processed, going through crushing and stamping stages to become a fine powder. This meticulous process ensures the clay achieves the required consistency and strength for the creation of durable and artistic pieces. The entire grinding process takes a considerable amount of time, about six hours daily to transform rough stones into fine powder, highlighting the dedication involved in the process.
Clay Preparation: From Powder to Mud
The fine stone powder undergoes a meticulous purification process. Running water separates the coarse particles from the finer ones, creating a clay slurry. This precise separation is essential for the strength and workability of the final clay. This slurry is then carefully transferred to several settling tanks, where the clay further refines.
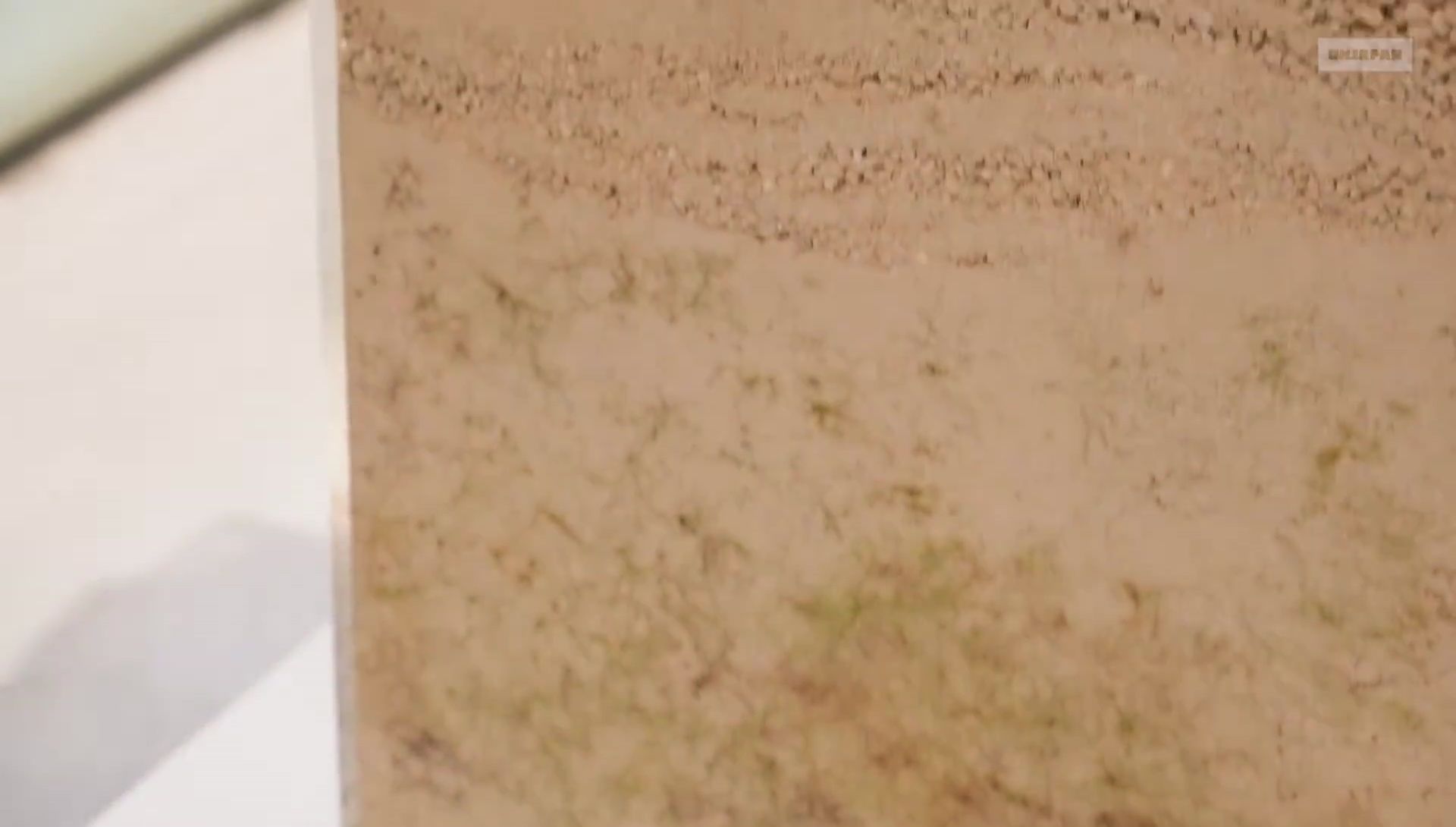
Three times, the clay is poured into settling tanks, allowing the finer particles to separate from any remaining impurities. This layered process significantly contributes to the superior quality of the finished clay. Finally, the refined clay is extracted and subjected to hydraulic pressure to remove any remaining air, creating a smooth and uniform material for the artisan’s craft.
Shaping and Decoration: The Artist's Touch
Once prepared, the clay undergoes shaping, a process that varies greatly depending on the artist and the desired piece. A variety of techniques are employed, including hand-forming and mold shaping, demonstrating the versatility of the clay and the skills of the artisans. This stage requires incredible skill and precision, each craftsman bringing their unique style and experience.
After shaping, the piece undergoes bisque firing at 900 degrees. This process leaves a distinctive pink mark on the surface if a specific technique is used. Following this initial firing, a coating known as "Yuyu" is applied, followed by a second firing at 125°C. Finally, the piece is painted and fired again, with the paint adding intricate detail and enhancing the already striking visual aspect.
Kutani Styles and Artists
The Cerabo Museum showcases a diverse range of Kutani styles and the works of talented local artisans. Pieces on display utilize various techniques, such as drawing patterns with seeds or connecting strands of gold, showcasing the ingenuity and creativity within this tradition. The museum highlights the rich history and skill involved in Kutani ceramic production.
The museum exhibits a wide variety of works, each piece reflecting the unique style and talent of its creator. From delicate and intricate designs to bold and striking patterns, the diversity of Kutani ware is on full display. The museum serves as a testament to the enduring legacy of Kutani ceramics and the dedication of its artisans.
Conclusion: A Legacy of Skill and Beauty
The creation of Kutani ceramics is a labor of love, a testament to generations of skilled artisans. From the careful selection and processing of raw materials to the intricate shaping and decoration, each step demands precision and dedication. The Cerabo Museum not only showcases the stunning beauty of Kutani ware but also provides valuable insights into the craftsmanship behind it.
The museum’s exhibitions demonstrate the versatility and enduring appeal of Kutani ceramics. The diverse styles and techniques employed ensure each piece is unique, showcasing the artists' skill and creativity. This museum offers a captivating journey into the rich history and ongoing evolution of this timeless art form, making it a must-visit for anyone interested in Japanese ceramics.